Quite often I receive requests to quote parts for diecasting and the purchaser may or may not realize what is involved in designing and fabricating a mold that will produce a quality die cast part in high volume quantities.
This is a brief overview of what a die cast mold is and how to approach the purchase of a new mold with a convenient checklist developed by the North American Die Casting Association. This checklist is a valuable tool to assist the purchaser and the die caster in making decisions in a concise manner during the product launch.
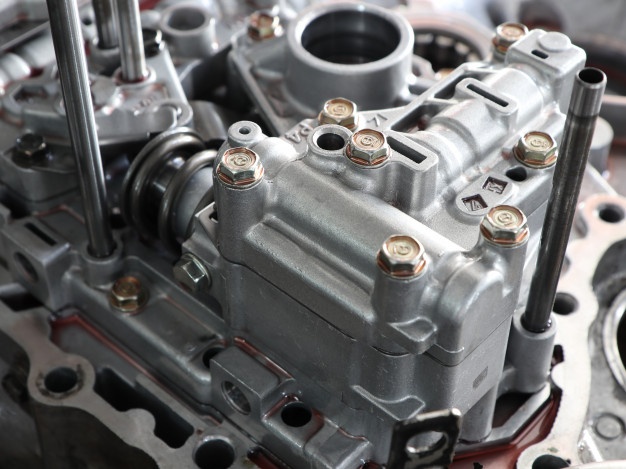
The Process
The diecasting die or mold is a closed vessel into which molten metal is injected under high pressure and temperature, then rapidly cooled until the solidified part is sufficiently rigid to permit ejection from the mold. Dies, or die casting tooling, are made of alloy tool steels in at least two sections, the fixed half (cover half) and the moving half (ejector die half), to permit removal of the castings. The dies also may have moveable slides, cores or other sections to produce holes, threads and other desired shapes in the casting.
A hole in the fixed die half allows for the molten metal to enter the die and fill the cavity. The ejector half usually contains the runners (passageways) and gates (inlets) that route molten metal to the cavity. Dies also include locking pins to secure the two halves, ejector pins to help remove the cast part, and openings for coolant to help cool the mold and solidify the molten metal.
A very important accessory required to run any die cast mold is called a Shot Sleeve. The Shot Sleeve is a hollow tube that is inserted into the hole in the fixed half of the mold when it is set in the die cast machine. The sleeve protrudes out from the die horizontally and there is a small opening in the top of the Sleeve where the molten metal is poured in preparation of the plunger injecting the metal into the mold. The Shot Sleeve needs replacement at certain intervals and is very important to the process. Quite often when molds are moved from a die caster, the Shot Sleeve is not sent with the mold which creates issues for the purchaser due to the lead time to fabricate a new Sleeve.
Making The Mold
The two die halves run in a die casting machine that is operated at the required temperatures and pressures to produce a quality part to net-shape or near-net-shape customer specifications. When the die casting machine closes, the two die halves are locked and held together by the machine’s pressure. The surface where the ejector and the fixed halves of the die meet and lock is referred to as the die parting line. The total projected surface area of the part being cast, measured at the die parting line, governs the clamping force of the machine.
For more information about Die casting malaysia, please visit https://stx.com.my/