Die casting tool, die casting machine, and die casting process are three key elements of the pressure die casting. These three factors are important factors to ensure the quality of die casting parts, improve the production efficiency of die casting parts, and reduce the production cost of die casting. When you choose the die casting process you may concern how much does a die cast tool cost?
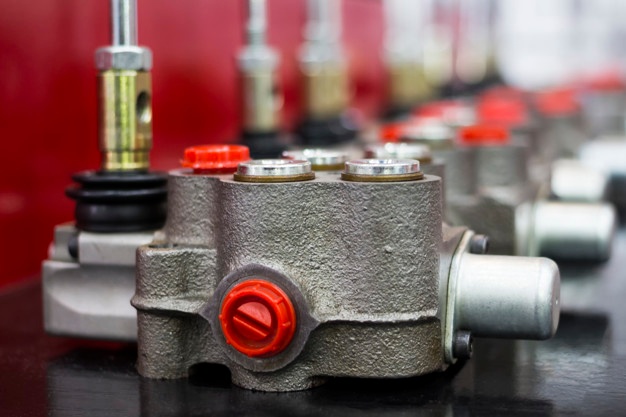
Main Components
The die cast tooling cost has two main components – the die set and the machining of the cavities. The cost of the die set is mainly controlled by the size of the diecast part. The part is larger the die set is larger and more expensive. The cost of machining the cavities is affected by nearly every aspect of the part’s geometry. The primary cost driver is the size of the cavity that must be machined, measured by the projected area of the cavity and its depth. Any other elements that will require additional machining work will add to the cost, including the feature count, parting surface, side-cores, tolerance, and surface roughness.
The tooling cost will be impacted by the tooling life which is affected by the number of diecast parts and the material we use. For example, materials with high casting temperatures, such as copper, will cause a short tooling life. Zinc, which can be cast at lower temperatures, allows for a much longer tooling life. This effect becomes more cost-prohibitive with higher production quantities.
One final consideration is the number of side-action directions, which can indirectly affect the cost. The additional cost for side-cores is determined by how many are used. However, the number of directions can restrict the number of cavities that can be included in the die. For example, the die for a part that requires 3 side-core directions can only contain 2 cavities. There is no direct cost added, but it is possible that the use of more cavities could provide further savings.
Die Cast Tooling Cost
A die casting tool cost is decided by those above factors. As a professional China die casting manufacturer, we will combine a variety of aspects to reduce costs for you and provide you with high-performance die casting products. Once you decide to choose the die casting process, pls contact us to tell us more detailed information and we will give you our best price.
The unavoidable fact is that die casting tooling costs are high, among the highest of any production process. This is because, due to the nature of die casting, the dies are subjected to exceptionally severe operating conditions over the course of normal service.
Factors Impacting Life and Costs
Tool material – Die cast tooling dies are tooled out of the highest quality engineered tool steel available, which is more expensive than standard steels but necessary for proper functionality.
Temperatures – Metal becomes molten at extremely high temperatures and introducing it to dies, no matter how good the quality of the die material, leads to some level of thermal shock and stress.
Die wash – Also known as die steel erosion, die wash is when metals with a tendency to attack tool steel flow over die surfaces, especially at irregular, small, or delicate die features.
For more information about Die casting malaysia, please visit https://stx.com.my/